Dive Deep: Insights About Aluminum Casting Processes
Dive Deep: Insights About Aluminum Casting Processes
Blog Article
Opening the Possible of Aluminum Spreading: Proven Methods for Success
Aluminum casting has actually long been acknowledged for its versatility and prevalent applications across numerous industries - about aluminum casting. Discovering the full capacity of this process calls for more than simply basic expertise. By implementing proven techniques refined with years of sector experience and innovation, suppliers can boost their light weight aluminum casting procedures to brand-new heights of effectiveness and high quality. From enhancing design factors to consider to enhancing production processes, the essential lies in using these methods successfully. Join us as we explore the necessary components that can move aluminum casting towards unrivaled success in today's competitive market landscape.
Advantages of Light Weight Aluminum Spreading
One of the primary benefits of aluminum spreading is its lightweight nature, which contributes to fuel efficiency in sectors such as automotive and aerospace. Additionally, light weight aluminum is highly malleable, allowing for intricate and complex shapes to be quickly produced via casting procedures.
Moreover, aluminum spreading provides exceptional rust resistance, making it optimal for applications where direct exposure to extreme settings is a concern. The material also displays great thermal conductivity, which is useful for markets requiring warm dissipation, such as electronic devices (about aluminum casting). Aluminum is fully recyclable, aligning with the expanding focus on sustainable methods in contemporary manufacturing.
Design Factors To Consider for Casting
The design stage plays a crucial duty in the general success of an aluminum spreading project. One crucial consideration is the choice of appropriate geometries and features that assist in the casting process.
In addition, considerations connected to parting lines, gating systems, and risers are important to avoid issues like porosity and shrinking. It is critical to optimize the style for reliable material use and reduce post-processing demands. Simulations and prototyping can be beneficial tools in fine-tuning the spreading and reviewing design before full-blown manufacturing.
Partnership in between layout engineers, foundries, and manufacturers is crucial to address any potential challenges early in the style phase. By incorporating these considerations into the casting layout procedure, manufacturers can boost item top quality, decrease expenses, and ultimately unlock the complete possibility of light weight aluminum spreading.
Enhancing Casting Performance
When intending to improve casting performance in aluminum spreading projects,Designing with an emphasis on maximizing material flow and reducing problems is crucial. To accomplish this, making use of simulation software program can help in recognizing potential issues prior to the spreading process begins. By simulating the circulation of liquified aluminum, developers can readjust gating and riser designs to make sure proper dental filling and solidification, inevitably reducing the incident of flaws such as porosity or shrinkage.
Additionally, applying appropriate warmth therapy processes can enhance the general casting effectiveness. Heat treatment can help boost the mechanical residential properties of the light weight aluminum spreading, ensuring that the last component meets the required specifications. Additionally, employing automation and robotics in the casting procedure can simplify manufacturing, lower hand-operated labor, and rise total performance.
In addition, continuous tracking and quality assurance during the spreading procedure are critical for recognizing any kind of deviations and guaranteeing that the end products fulfill the preferred requirements. By executing these methods, makers can improve casting efficiency, boost item high quality, and ultimately attain greater success in aluminum spreading jobs.
Quality Control in Light Weight Aluminum Casting

Effective quality control techniques play an essential role in ensuring the precision and reliability of light weight aluminum spreading processes. Quality control measures in light weight aluminum casting incorporate a range of tasks aimed at supporting details requirements and identifying variances that could compromise the last product.
In addition to process control, quality control in aluminum casting involves rigorous screening and assessment treatments at different stages of production. By executing robust quality control methods, aluminum casting facilities can supply items that satisfy client expectations for dependability, quality, and performance.
Optimizing Earnings
To achieve optimum economic performance, a comprehensive strategy for making best use of profitability within light weight aluminum casting more procedures should be meticulously devised and implemented. One essential facet of making best discover this info here use of success in light weight aluminum casting is maximizing manufacturing effectiveness. This involves enhancing procedures, decreasing waste, and minimizing downtime to guarantee that sources are used effectively. Carrying out lean manufacturing principles can aid identify areas for renovation and enhance total operational effectiveness.
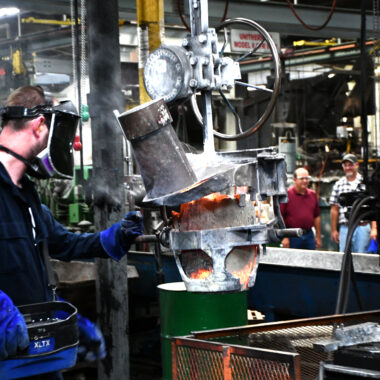
Moreover, branching out item offerings and exploring new markets can aid increase income streams. Comprehending consumer requirements and market fads can guide tactical choices to profit from emerging chances. Buying r & d to introduce items or procedures can also drive success with distinction and customer contentment.
Conclusion
To conclude, light weight aluminum spreading offers various benefits in regards to style toughness, cost-effectiveness, and versatility. By very carefully taking into consideration layout factors to consider, improving casting effectiveness, executing quality control measures, and taking full advantage of success, suppliers can open the full potential of light weight aluminum casting. This trusted and functional process has actually verified to be a successful selection for a variety of commercial applications.
Furthermore, aluminum is highly flexible, allowing for complex and complex shapes to be conveniently produced with casting processes.Effective quality control techniques play a critical duty in guaranteeing the precision and dependability of aluminum casting procedures.In addition to procedure control, top quality control in aluminum spreading includes strenuous testing and assessment procedures at different phases of production. By executing durable high quality control techniques, aluminum casting centers can supply products that satisfy consumer assumptions for performance, dependability, and high quality.
By meticulously considering layout considerations, enhancing casting effectiveness, carrying out high quality control actions, and optimizing productivity, suppliers can unlock the full potential of Click This Link aluminum casting.
Report this page